In February 2020 a team made up of two textile conservators, the touring manager, and a collections technician travelled to Sweden to install National Museums Scotland’s first international touring fashion exhibition, Body Beautiful – Diversity on the Catwalk, at the Textilmuseet in Borås, Sweden.
The install was the culmination of months of hard and dedicated work to prepare 26 mannequins for upright and flat travel. During the preparations, there were countless unknown factors about how the mannequins would travel. Would they be supported? How might they move along the way? And would the potentially freezing Swedish weather be a factor?
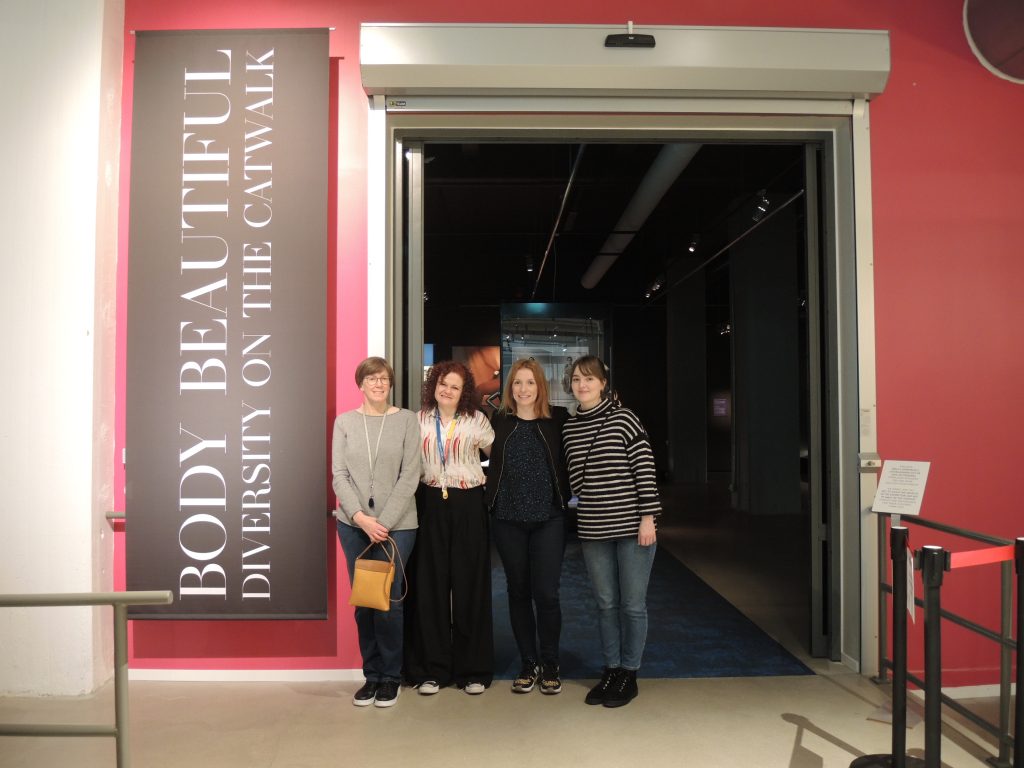
team at the entrance of the freshly installed exhibition in February, 2020
Once the dust had settled (not on the objects), the crates had been packed away and the last Fika (tea and cake) with the Swedish team had been had, we headed to the airport to make our way back to Scotland. Reflecting on a successful but exhausting install, there was a slight air of unease as the first whispers of COVID-19 began to float. Little did we know that the forthcoming global pandemic would prevent us from returning to de-install the exhibition we had just worked so hard to install.
Fast forward to August 2020 and – after investigating how other museums were handling remote management of their objects on loan and tour – we decided that the only way we could de-install the exhibition was to do it virtually. Unlike the UK, Sweden had been relatively unaffected by institutional closures during the COVID-19 pandemic and were keen prepare the space for the next exhibition.
Taking shifts to be virtually present during the de-install from the home office. A laptop perched on jigsaws boxes: a 2020 home-working trend.
During the install, we saw first-hand the team at Textilmuseet’s understanding and experience of handling textiles – particularly costume – and we felt confident that they would be capable of managing the unchartered territory of de-installing remotely. The initial familiarity and teamwork helped us make the decision to allow them to handle and prepare the objects for travel, which was key to its success.
On top of the Swedish team’s extensive experience, the National Museums Scotland conservation team had worked tirelessly to write hyper-detailed documentation for each object. Every garment had specific conservation packing needs which were individually recorded. In addition, each had thorough packing, unpacking, mounting and crate packing instructions and its own detailed condition report.
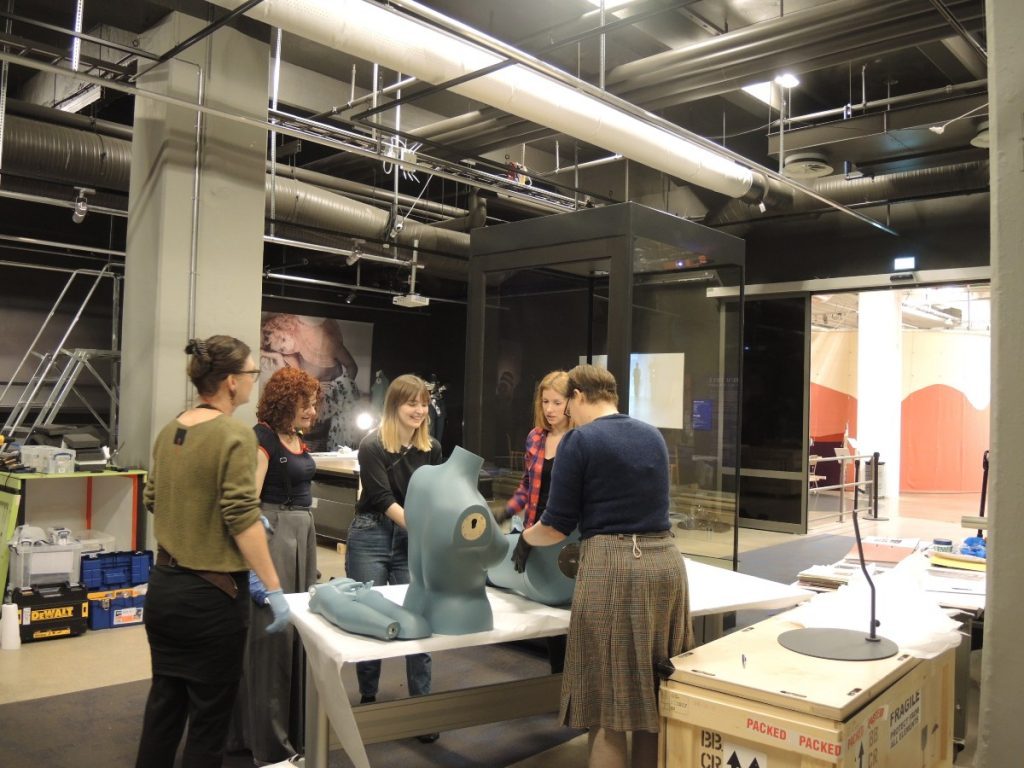
We had written these with such intense detail that, initially, it was thought they would be tedious to read and unnecessary as we already knew the objects inside out. Fear of the unknown got the better of us and the (small) risk of not being able to attend the de-install far outweighed the labour-intensive process of writing them. Little did we know how vitally useful this risk assessment would turn out to be!
My line manager – Principal Textile Conservator, Lynn McClean – and I worked in shifts to be present via video link to virtually observe and manage the de-install of the exhibition. Our colleagues in Sweden were able to position the camera, enabling us to view and advise on how to safely pack and move the various mannequins and garments. They used our written instructions to remove and pack the garments step-by-step whilst we watched and were able to advise when they had any issues. They said they were initially overwhelmed by the volume of our instructions, but on completion said they couldn’t have de-installed the objects without such acute attention to detail.
Installing the FTL Moda Chain Dress De-installing and packing it using written instructions.
There were essentially three different types of objects to de-install – the ‘upright mannequins’, the ‘flat-packed mannequins’ and paper invitations, magazines and framed prints. The upright mannequins travelled dressed, with any elements at an increased risk such as shoes, accessories and removable heads all packed separately. In order to ‘pack’ the uprights, the mannequins had to be removed from display and placed into individual crates once the relevant padding and packing materials were put in place to protect the objects.
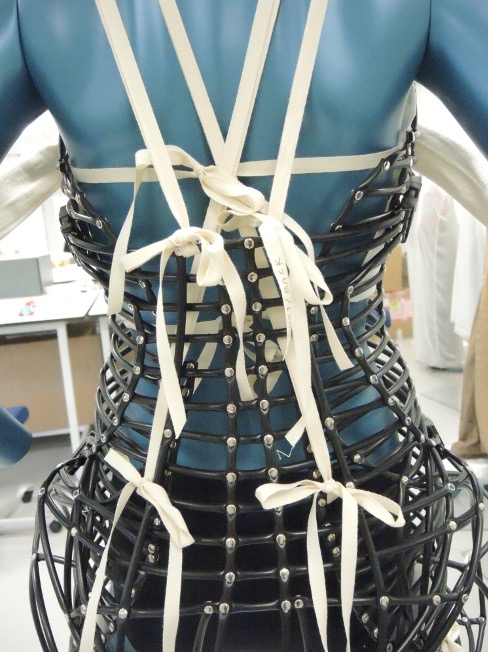
Whilst this sounds straightforward, the team in Sweden were tasked with ensuring that the objects were packed safely and securely using our detailed instructions to replace and position elements down to the minutia. For example, the mannequin for the FTL Moda cage dress required specific instructions to weave cotton tape straps in and out of the latticed structure to ensure that it was supported correctly. Any errors may have resulted in the dress dislodging and the rubber tubes rubbing against the mannequin, potentially leading to damage.
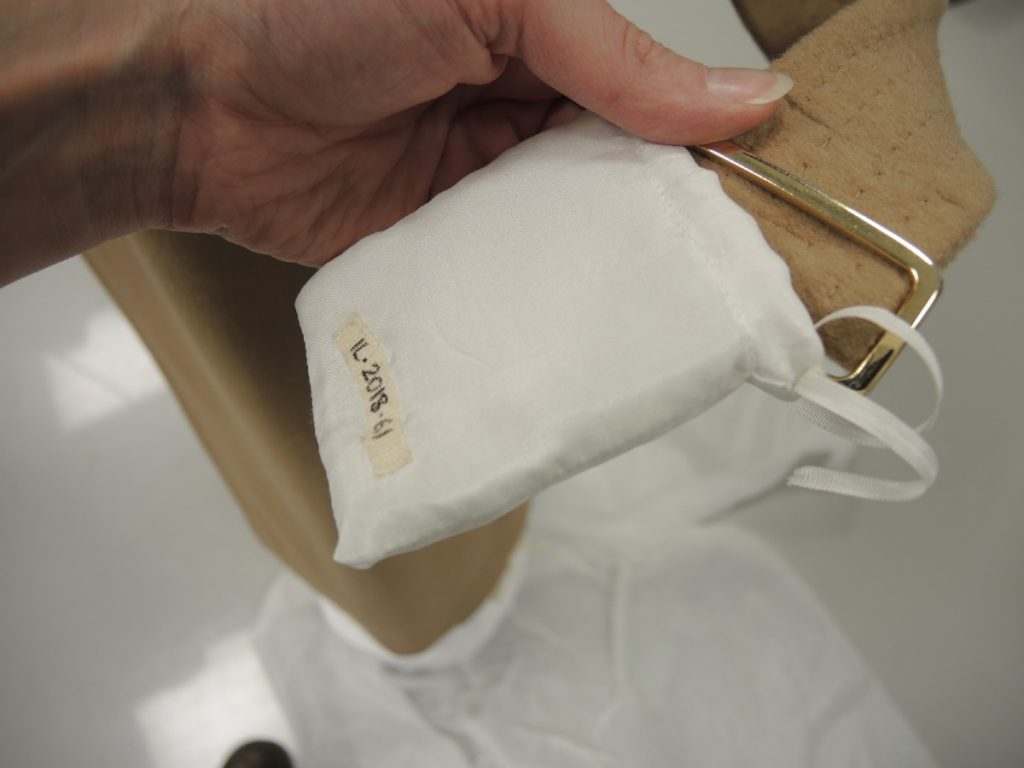
On one end of the scale, we had upright objects which were highly susceptible to damage during travel. These needed protections ranging from miniature padded silk bags for belt buckles and buttons to friction reducing padding and props to prevent folds. At the other end, some objects were relatively low risk, only requiring basic silk arm bags, a silk garment bag and a Tyvek® cover. Whether simple or complex, the team in Sweden managed to follow the written instructions to the letter and each object was packed safely.
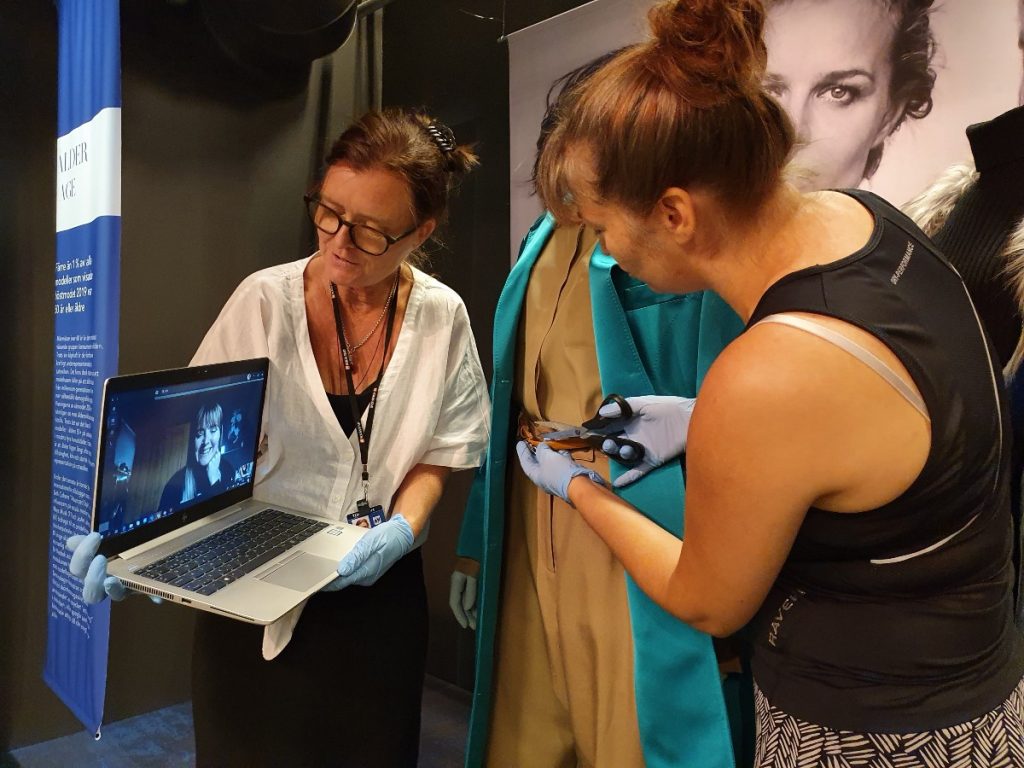
Flat-packed mannequins required a different method. These garments needed to be removed from the mannequins and packed separately into boxes. This sounds straightforward, but each of the flat-pack boxes was equally, if not more, complex than the upright mannequins.
Each individual component of the ‘look’ had to be unhooked, dismantled, or detached piece-by-piece. This can be a very tricky process indeed, sometimes requiring a mannequin arm to be removed before the garment itself. Flat-packed objects had to be neatly nestled back into their custom-made boxes with recesses, straps and fastenings, and mannequins had to be dismantled, wrapped and packed back into their boxes. As well as written instructions, we also filmed and sent over video instructions on the best way to dismantle the mannequins!
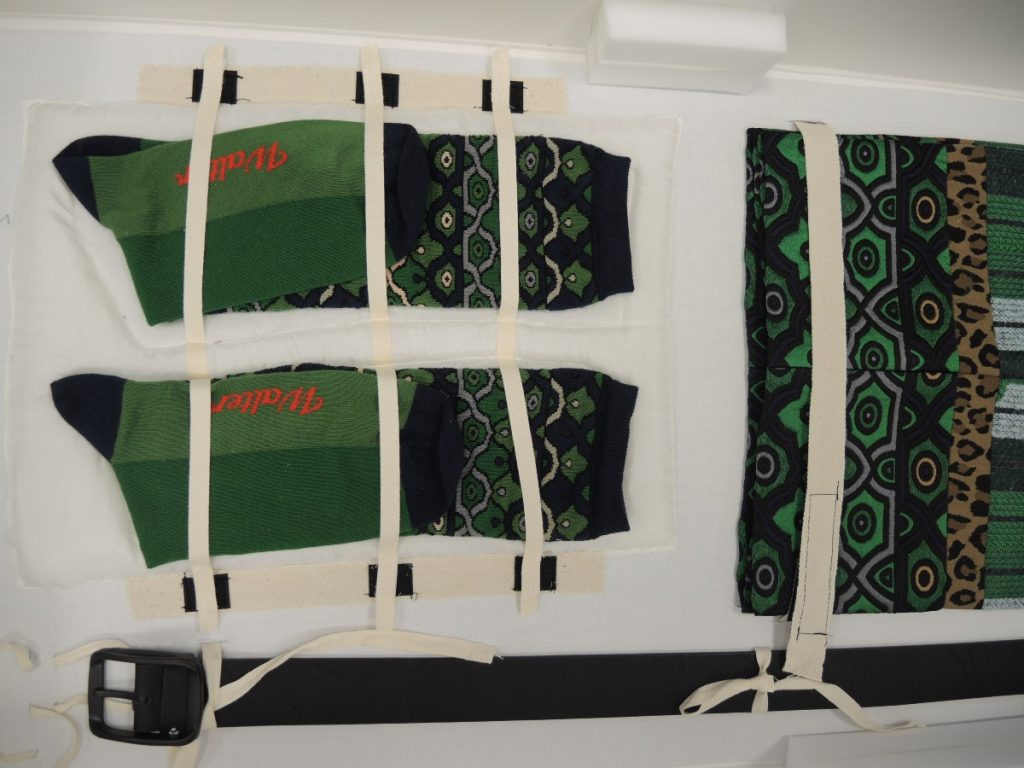
The success for us throughout the de-install of Body Beautiful hinged on excellent communication. Whether that was through video link, verbal, or written communication, it was essential to maintain dialogue to overcome the challenges of not physically being present – particularly when it came to the de-installation of the paper objects, which we all had limited experience with.
Although we managed a successful de-install from across the North Sea, it was not without its challenges. We were aware that internet connections had to remain stable and we had to have the ability to vocalise any issues or difficulties if we needed to express how something needed to be done. At times, it was tricky to be so visually mobile and stationary at the same time leading to a small amount of motion sickness – which was surprising! For the most part we had managed to consider almost everything beforehand, giving us an excellent framework for future virtual exhibition management.