Nearly a metre in length, 250 years old and broken into two shattered halves, the James Bruce drinking horn represented an epic challenge in my conservation career. This is the conclusion of the horn’s incredible conservation journey.
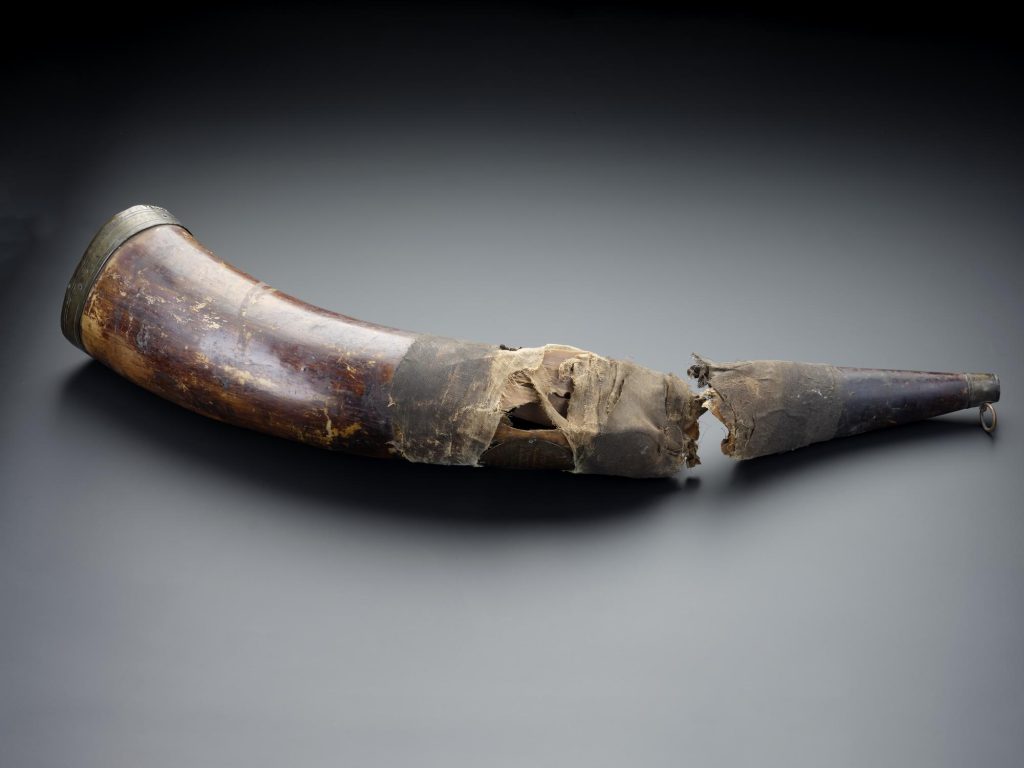
After my initial assessment and extensive cleaning processes described in the previous blog post, I had to move on to the more complicated – and in some ways more exciting – conservation tasks. First, this meant the stabilisation and reshaping of horn material before I could finally mend the two halves and fill in all areas of loss. Each step on the journey felt like reaching a new level in a video game!
No move without water – Stabilisation and reshaping
Both the stabilisation and reshaping measures seemed at first to be separate processes, but in practice I found they were often intertwined. For example, whilst I consolidated delamination, I also reshaped these areas at the same time by pressing the material back in position.
The two measures had another thing in common – the necessity to soften the horn material prior to any intervention to make it flexible and responsive. I achieved this through a humidification process by simply applying a moist fabric onto the horn’s surface. Depending on the task and thickness of the horn material, I humidified areas between two hours (for the adhesion of delaminating top layers) and up to 16 hours overnight (for reshaping areas of thick and sturdy horn material).
Consolidation of delaminating material
Before I could tackle the distortions and large cracks in the horn, I had to turn the crumbly, paper-thin layers back into a compact sheet of horn material. From my last post, you will recall the most severe case of the horn resembling filo pastry was in the area of the old fill. Here the material broke down in countless thin and brittle layers. Delamination also occurred along the break edges and on the inner surface of the horn.
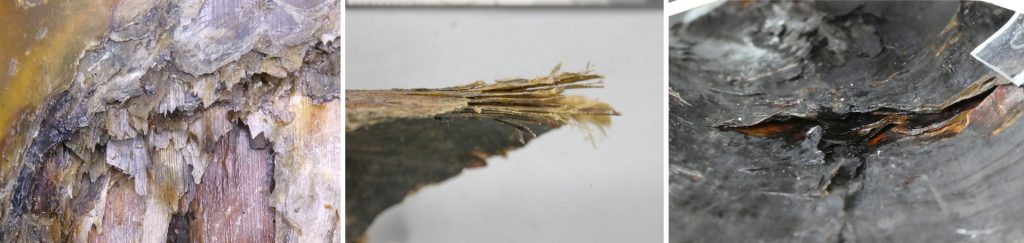
To consolidate the layers, I decided to use a protein glue. This glue is water based and was well-matched to the entwined reshaping process which required ongoing humidification. A water-based adhesive can react, adapt to slightly changed shapes and harden out again in the new position.
I chose bone glue, as it will be strong enough to recreate a rigid and stable horn sheet and withstand the pressure I will need to apply during the reshaping process. A weaker protein glue would have failed halfway through the procedure. Even with the bone glue, it was often a balancing act to keep the bonds stable.
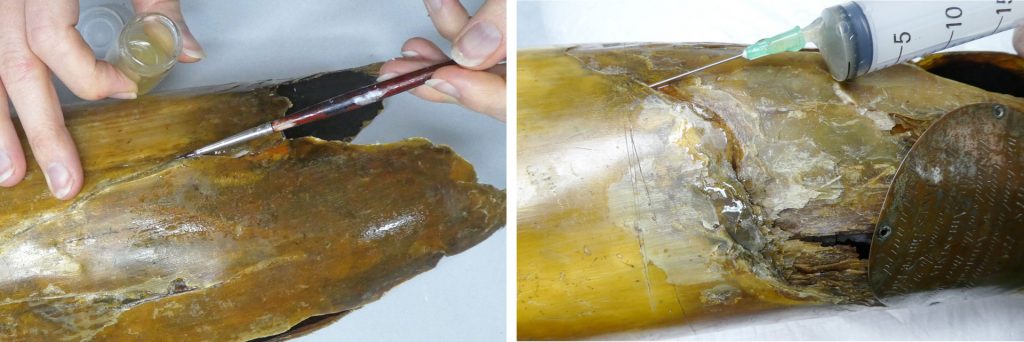
I applied the adhesive with a brush or a syringe between delaminating layers. The drying process could take up to 12 hours and, during that time, the layers had to be pressed tightly together. This required different techniques in different areas, and I had to be inventive to apply the pressure I needed. Below you can see some of these methods.
Consolidation of break edges
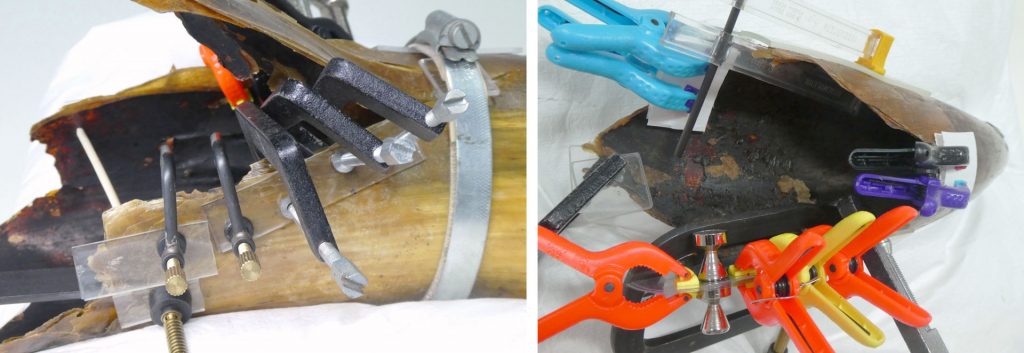
The consolidation of material along break edges was relatively uncomplicated. I had clamps of various types available, just sometimes not as many as I wished.
Consolidation of inner surface
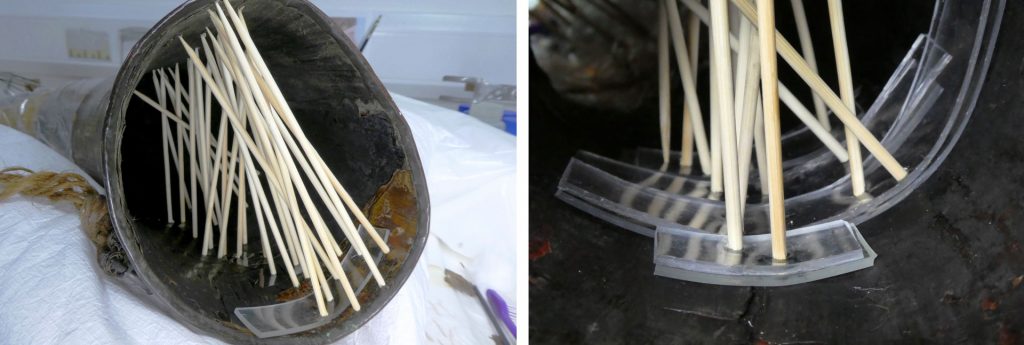
These areas were out of reach for my clamps. In similar cases, I had successfully worked with the Japanese shimbari technique and went about adapting the technique with the horn. I placed bamboo sticks with one of their ends on the area to be pressed down and then tightened the sticks by securing the other end to the opposite side of the inner surface. To evenly spread the pressure, I used PVA sheets as interlayer. In a few days I was able to build an impressive construction in the horn’s cavity.
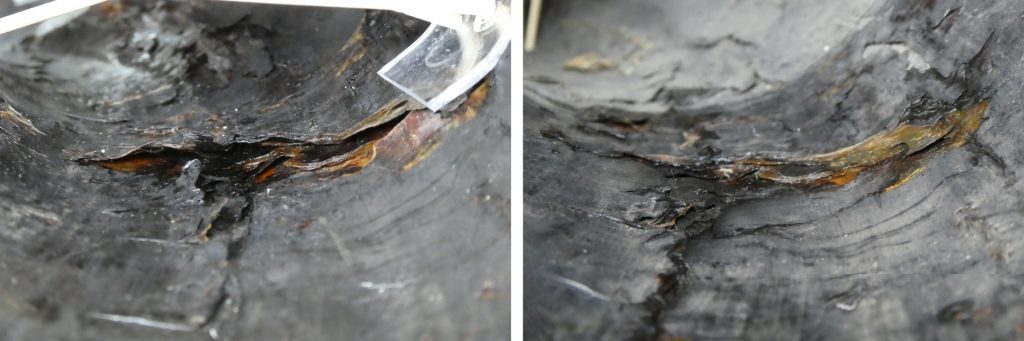
I let the areas dry overnight, took the sticks out the next day and removed excess of glue with a small amount of deionised water on cotton swabs.
Consolidation in area of old fill
In the area of the old fill the horn material was not only extensively frayed but also pressed inwards. To bring the material outwards again I required a heavy-duty clamp and, most importantly, custom-made wooden blocks shaped to precisely follow the original curve of the horn (convex for the inside or concave for the outer side).
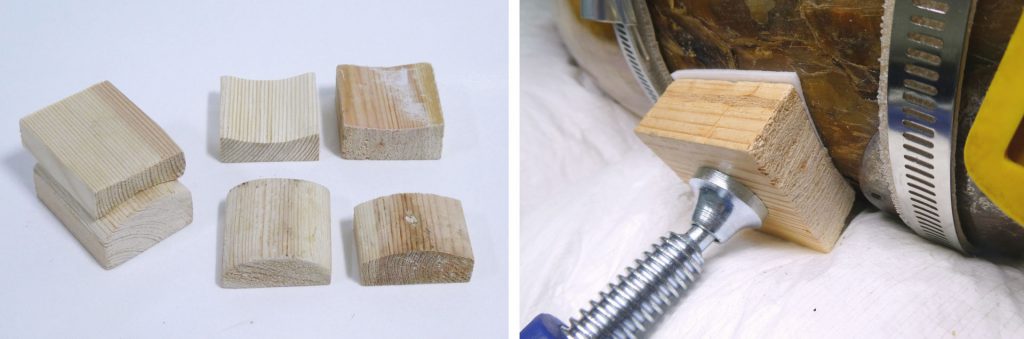
After injecting the adhesive in between the horn layers, I sandwiched them between my custom-made blocks. Using a C-clamp I pressed the blocks, and with it the horn material, tightly together. These moulded and lifted the inwards collapsed material back into its original position.
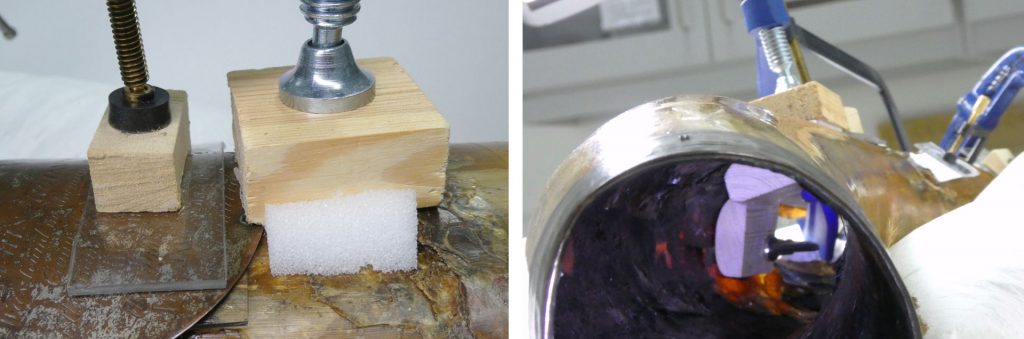
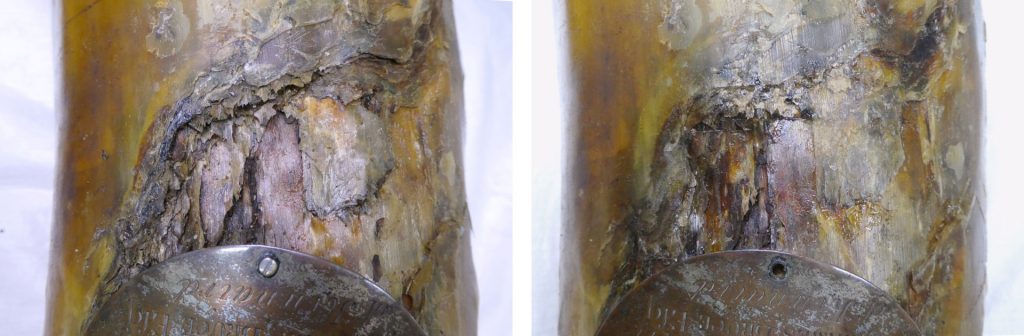
Reshaping
For the reshaping process I humidified the horn material over large areas overnight to give the water enough time to penetrate in to deeper layers and achieve a higher flexibility. The next day, I applied various clamps and my custom-made blocks to push the horn back into its original shape.
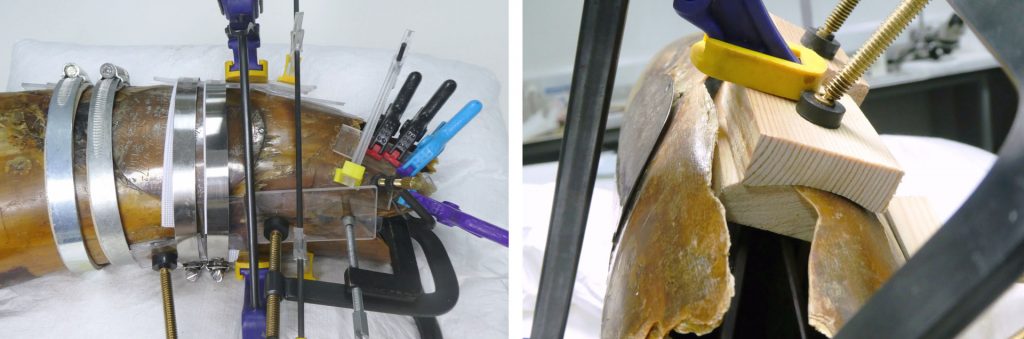
I left the clamps in place over night to ensure the horn material has fully dried and regained its sturdiness. Unfortunately, it’s not possible to remove such severe distortions in one go. The material must gradually re-learn its original form. Therefore, I had to repeat the process between five to ten times per area, which made this step the most time consuming. It took around two months to reshape the entire horn in this way. However, it was worth the wait and it was very satisfying to see the original diameter of the horn become reinstated and the broken edges along both parts realign.
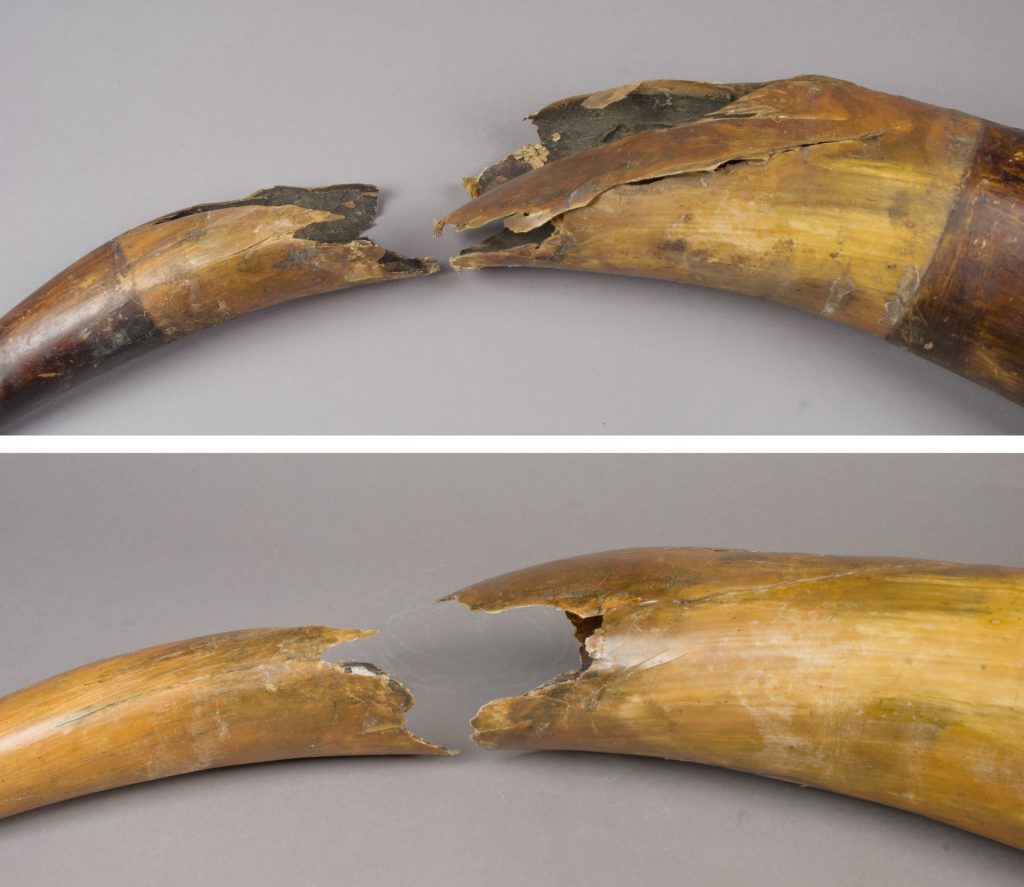
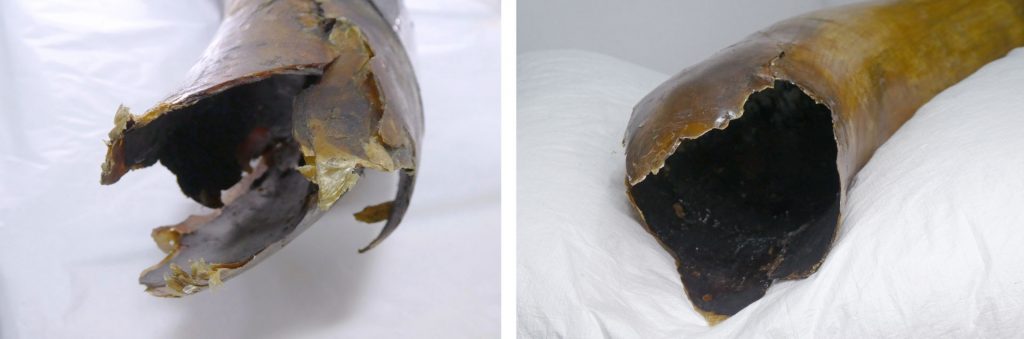
That said, in a few areas it wasn’t possible to achieve a full recovery of the original shape. This was the case in the area with the matching break edge. Here, I managed to reshape the material along the crack so that it was no longer overlapping, but it was still not enough to attach the other piece, which was frustrating (especially for a perfectionist like myself!)
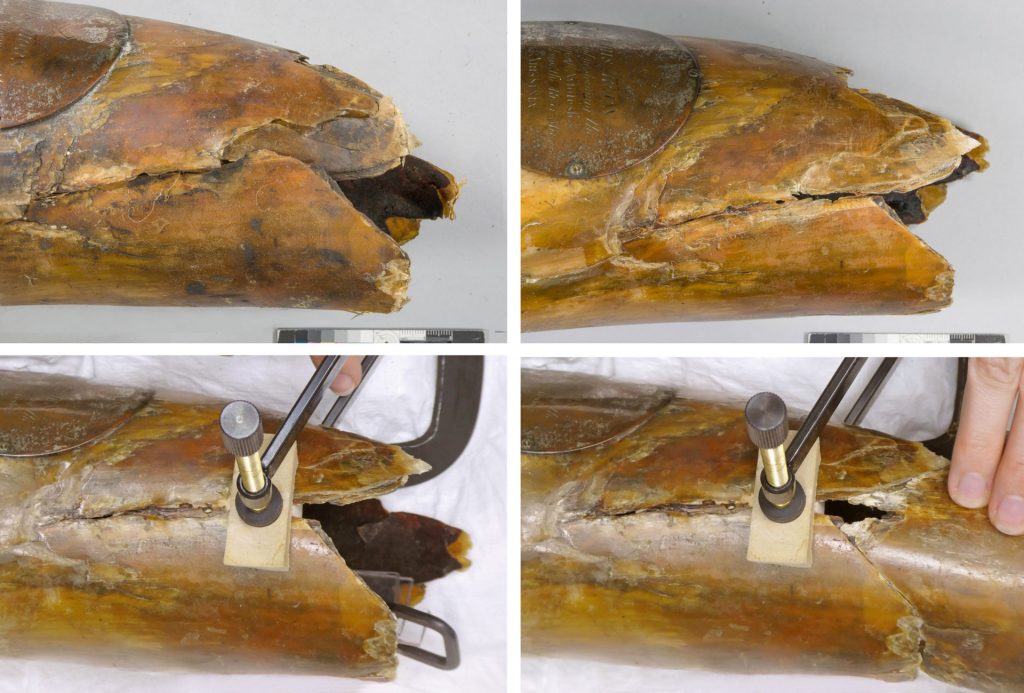
Finally, I used a clamp to overcome the remaining tension and keep the material in the desired position. But this could only be a temporary solution. What could I do to keep the material in check while attaching the other part?
Mending the pieces – An inner cast for the broken horn
To mend both pieces, I needed an inner cast for the broken horn. I found everything I needed in X-Lite. X-Lite is used – quelle surprise! – in the medical sector to cast broken extremities. It is made of a 100% cotton mesh, which is impregnated with a non-toxic thermoplastic resin.
I activated pieces of the mesh in a hot water bath before quickly applying each piece to the inner surface of the horn. By applying multiple overlapping layers, I increased the rigidity of the material and, in a relatively short amount of time, I had built a complex inner support out of four layers of X-Lite.
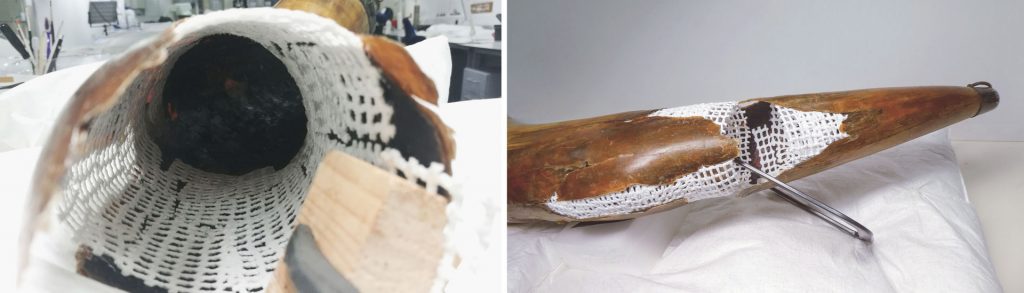
This process provided such a high level of rigidity and support that I was even able to support the matching break edge. When I removed the clamps, I held my breath but the material didn’t collapse inwards again – I felt so relieved! The highlight was the moment I mended both parts with this material and closed the last gap in my support. I captured this process in the timelapse video below:
What you can’t see in the video is how complicated it was to close the last gap. For this, I had to access the horn from its opening – which was around 60 cm away from the area, and my arm is only 50 cm long! I could reach the area with the spatula but then couldn’t see what I was doing. The solution? An endoscope camera to cast a live image of the area to my laptop. It really felt like carrying out endoscopic surgery!
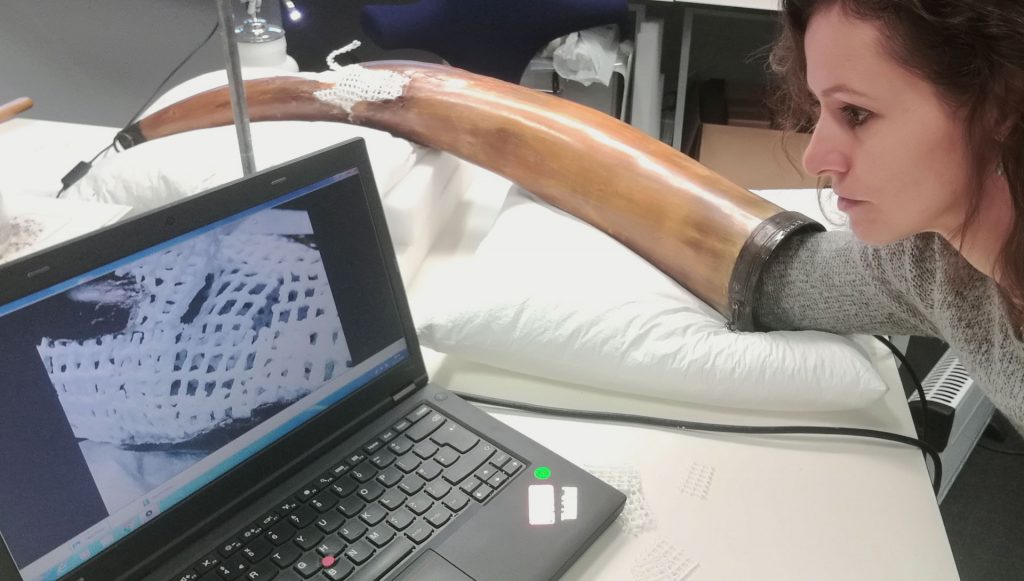
Filling the areas of loss – 50 shades of brown
After its stabilisation I was happy to see the horn back in one piece. The intense pressure and stress fell off my shoulders. It worked out! Now I was able to see how much of the horn material was actually missing.
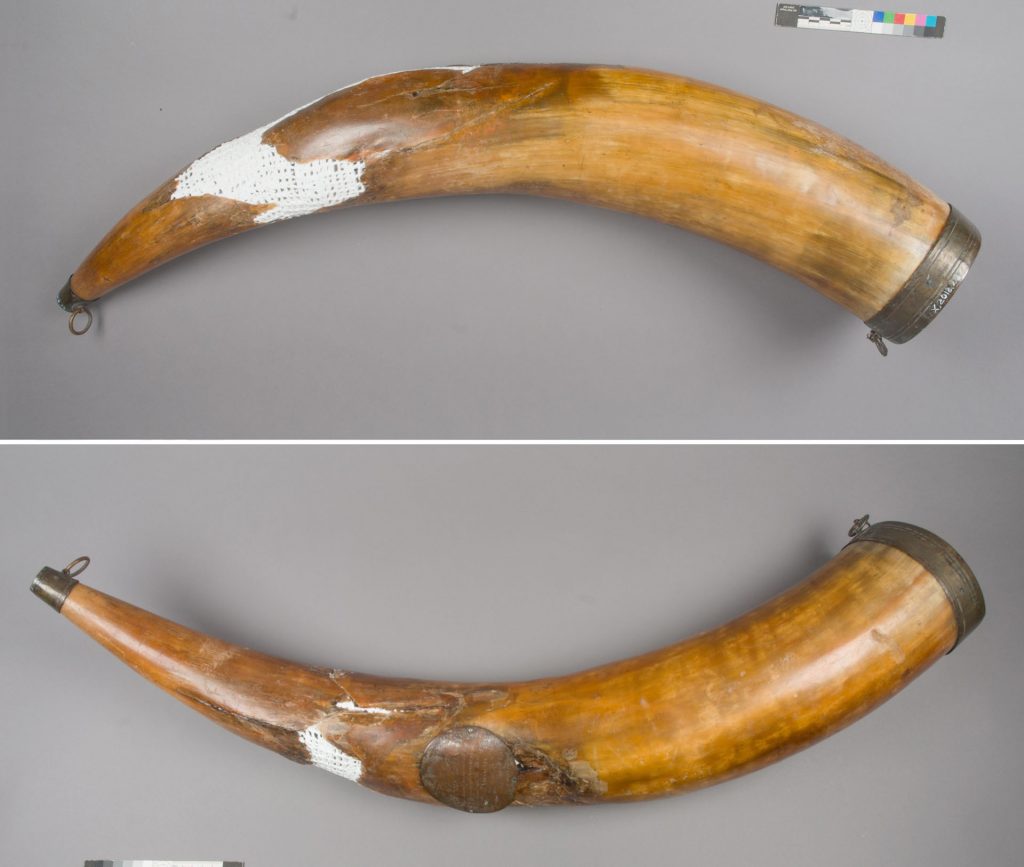
The white X-Lite mesh contrasted to the light brown colour of the horn but, despite my pride in the work I had done with the support layer, I didn’t want the repair to outshine the object itself. Conservation measures need to be discreet and I looked for a filling material which matched the various colours, opacity and sheen of the horn, whilst also being identifiable and having a certain elegance itself.
I tested various materials to achieve the desired fill. My first choice, the acrylic adhesive Paraloid B72, didn’t work as it is very time consuming to cure sheets without creating air bubbles and to mould the sheets into position. My tests with BEVA gel (Berger’s ethylene vinyl acetate) also failed due to high shrinkage. Epoxy resins achieved the desired colours and opaqueness but were too runny to apply on curved surfaces. I considered moulding and casting the missing areas, but again I didn’t have enough time to develop a successful system.
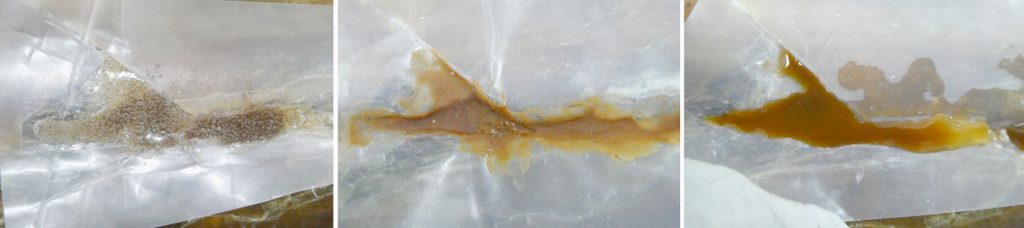
In the end I moved away from Paraloid, Epoxy resin and BEVA gel and followed the advice of my colleague Charles to use BEVA film. Free of solvents, the dry and transparent BEVA film eliminated the risk of shrinkage that comes with the gel. As the material is a thermoplast, I could melt it and mix in a different pigment ranging from yellow ochre to raw umber to create coloured discs. I then mixed various ratios of these together to create a wide range of hues in brown and ochre.
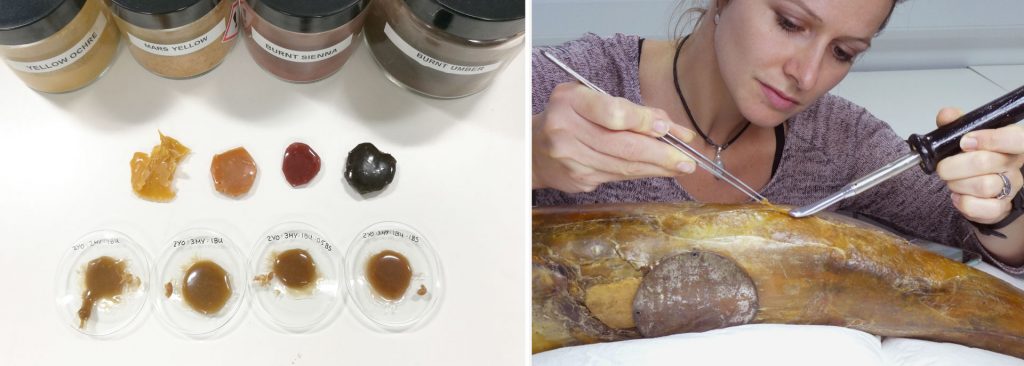
I used small cuttings of these and melted them in place with a heat spatula. As the material becomes gooey when heated up, it felt like inpainting with various hues of toffee and the process is super fun! This timelapse captures the process in one area:
The fills took me more than a week, but the result was very satisfying as I was able to reproduce the various colours and surface finish of the horn. I’m satisfied the fills blend in with the original surfaces very well and make my many processes and fixes as discreet as possible.
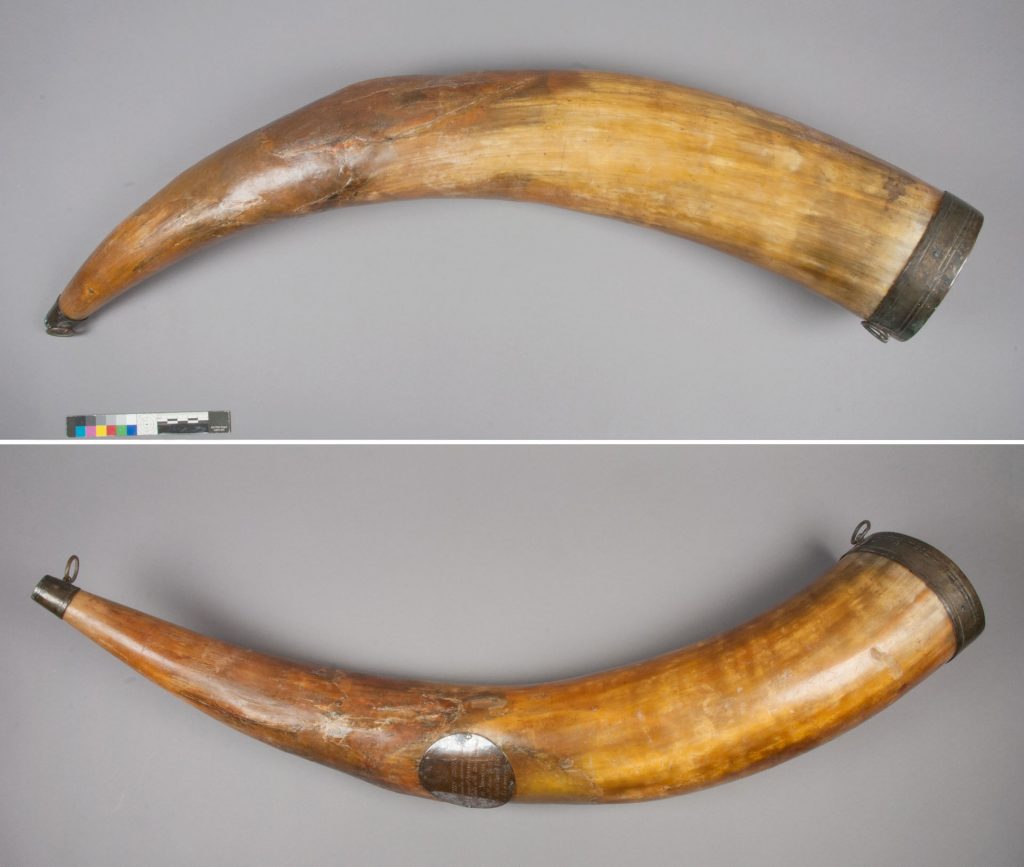
Reflections
I still tend to see flaws in my work, such as the areas I couldn’t fully reshape. What helps me though is to look back at images of the horn before I started the conservation and then review the entire process. Doing this with the drinking horn has made me really appreciate my work and my approach of finding the best solution at stage – and never doing anything by halves! As the horn left the conservation studio to be installed in the Legacies of Empire exhibition I can honestly say I’m very proud to have achieved the result I did.
Charting progress: The horn through different stages of the conservation process.
I hope you’ve enjoyed joining me on this conservation journey, and found the transformation process – summed up in the images above – as satisfying as I did!
Watch the video below to see the whole process start to finish.
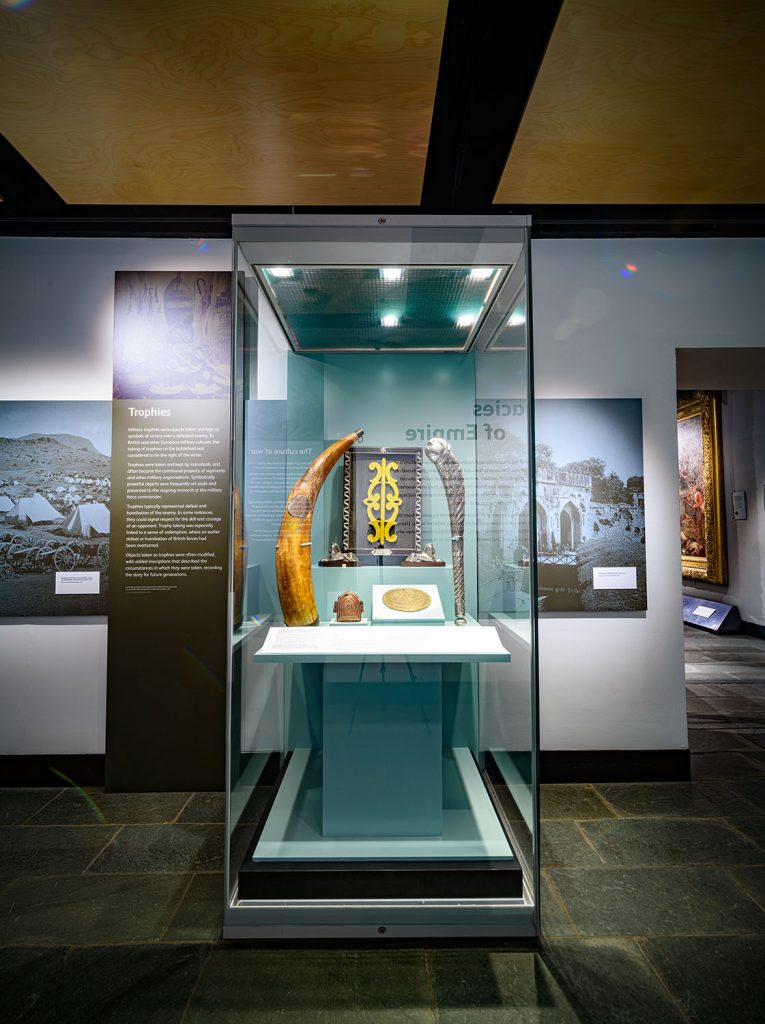
See the drinking horn
The James Bruce drinking horn displayed in the Legacies of Empire exhibition, National War Museum, 27 November 2020 until 30 January 2022.