This unusually shaped hat was conserved for display in the Exploring East Asia gallery, which opened at the National Museum of Scotland on 8 February 2019. Known as a ‘samo’, it would have been worn by a Korean court official in the late 19th or early 20th century.
The hat is made of stiffened paper with a mesh of narrow strips of bamboo at the front and at the upper back. The whole hat is covered with a very fine black silk fabric. Two ‘wings’ of horsehair are attached to the back, which is higher than the front.
The front of the hat before conservation. The back of the hat before conservation, showing the attachment of the ‘wings’.
The construction and poor condition of this hat posed numerous challenges for the conservator. The front mesh has sustained extensive damage; there is a long ‘L’ shaped split in the mesh which runs horizontally between the high and lower part of the hat then down the centre front with a large area of loss in the silk fabric covering. There is a horizontal break in the slightly thicker mesh at the back of the hat, with an area of loss in the silk fabric. The silk fabric overall is extremely fragile, with many worn areas.
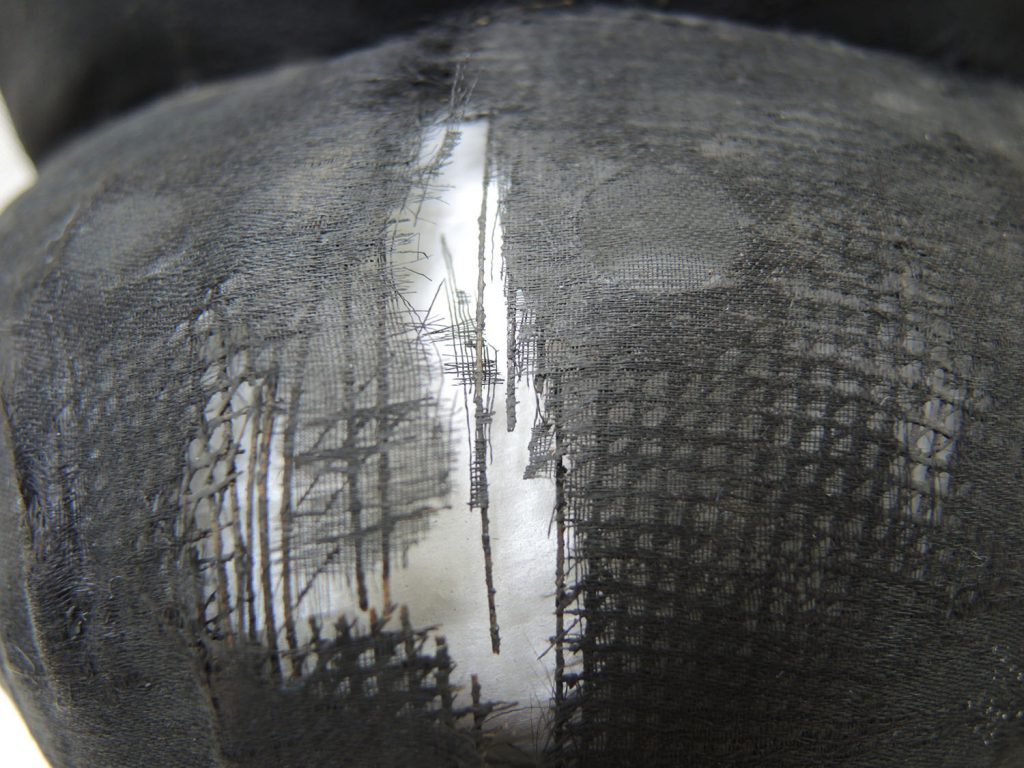
The first stage of conservation treatment was to stabilize the mesh at the front of hat. After considering several options, it was decided to use a mercerised twisted cotton thread that was coated with a black acrylic paint to produce a stiffened black strand of appropriate thickness. Small pieces of the thread were cut to the required size and used as splints to make essential repairs to the mesh. An adhesive dissolved in solvent was used to attach the splints. A tiny spot of this quick-drying adhesive was applied by brush to the ends of the thread splint, then the splint was positioned onto the inside of the mesh using tweezers.
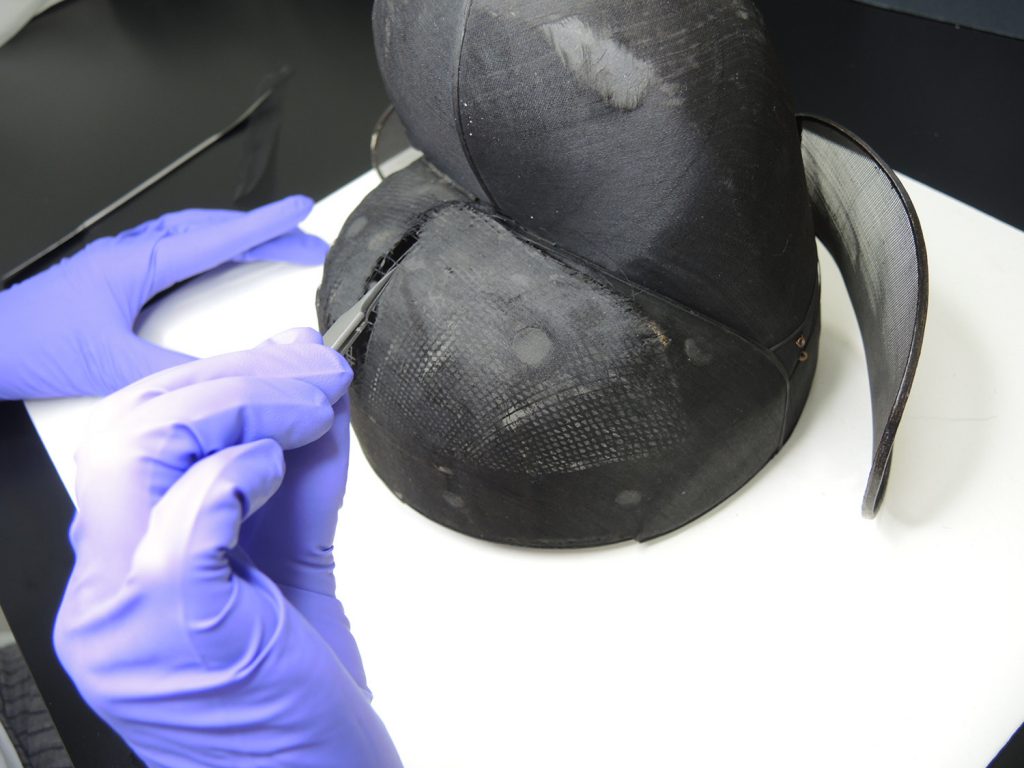
Once the structure was sufficiently stable, options for the conservation of the damaged fine silk were considered.
The front and back of the hat were treated differently. As the silk fabric at the front was extensively damaged and fragile, it was decided to apply a protective overlay of silk crepeline fabric dyed to a matching black. A soft tissue pattern of the front part was made and then transferred to the silk crepeline. The cut edges of silk crepeline fray readily, so it was first coated with a very dilute solution of a modified cellulose adhesive. When dry this is not apparent, but helps to prevent fraying and keep the warp and weft aligned, thus making the silk crepeline easier to work with. The silk crepeline was attached to the front part of the hat by adhering around the edges only, applying slight tension to ensure the overlay lies smoothly. A thermoplastic adhesive was used, which was activated using a heated spatula.
Silk crepeline laid over the front of the hat, secured to the narrow groove between the front and the back. Adhesive applied to the lower edge of silk crepeline was heat activated with a heated spatula.
The damaged mesh on the back of the hat was treated in a similar way to the front, although thicker splints were required. Narrow strips (approximately 5 mm wide) of Japanese paper were coloured with black acrylic paint. Once dry the strips were twisted to form fine splints and used to make repairs to either end of the break. Loose areas of silk fabric on the crown of the hat were secured using a small amount of adhesive dissolved in acetone This was brushed onto the solid base of the crown with a fine brush and the loose silk gently pressed onto the adhesive. As the adhesive is dissolved in acetone it didn’t cause wetting of the substrate and dried quickly.
The partially detached silk on the left of the hat was secured to the mesh by laying very fine silk threads across the silk fabric.
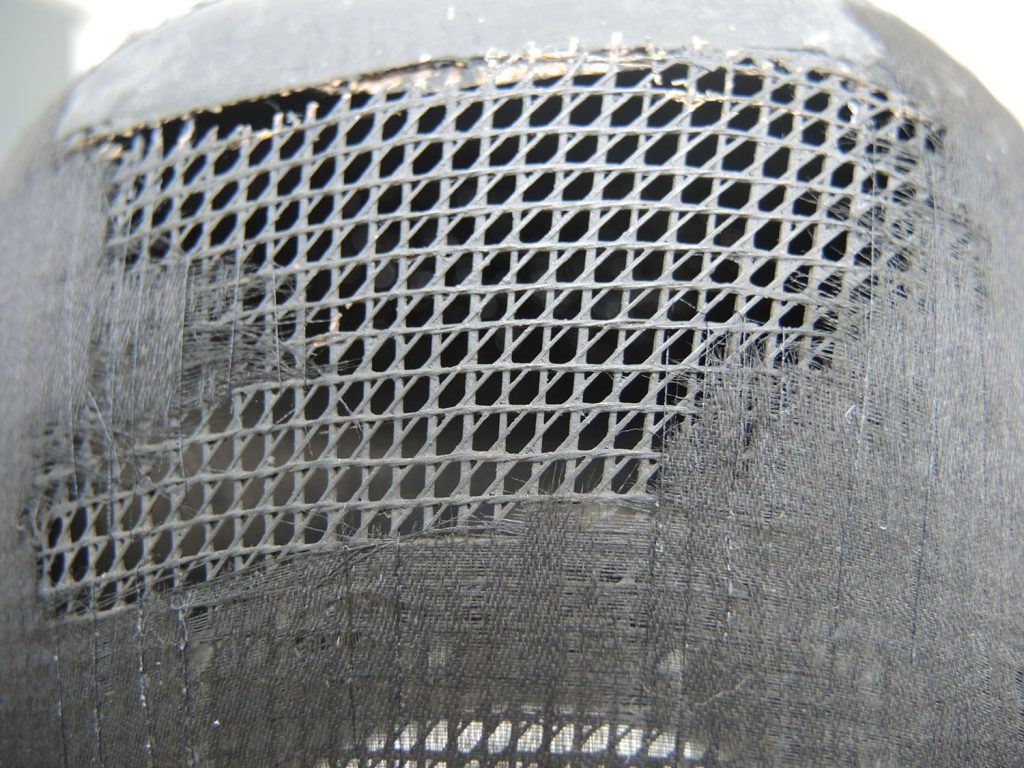
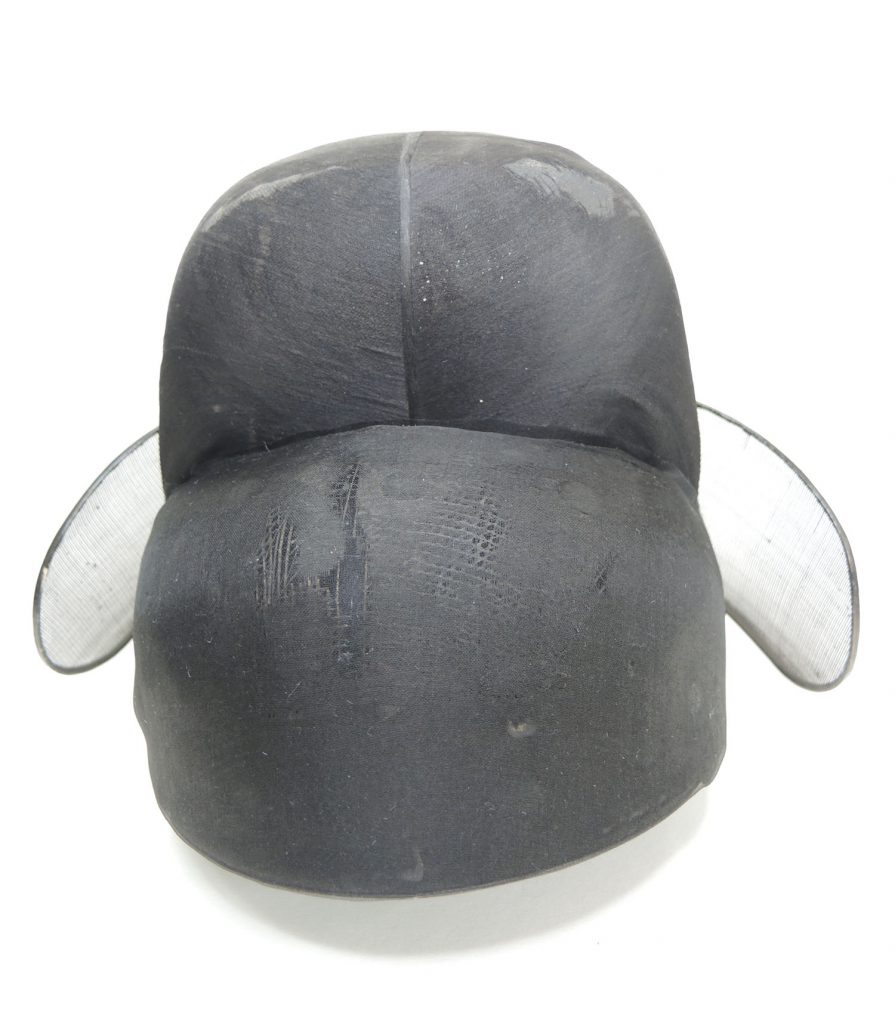
Although this was a complicated treatment, it has made the Korean hat safe for display in the Exploring East Asia gallery.